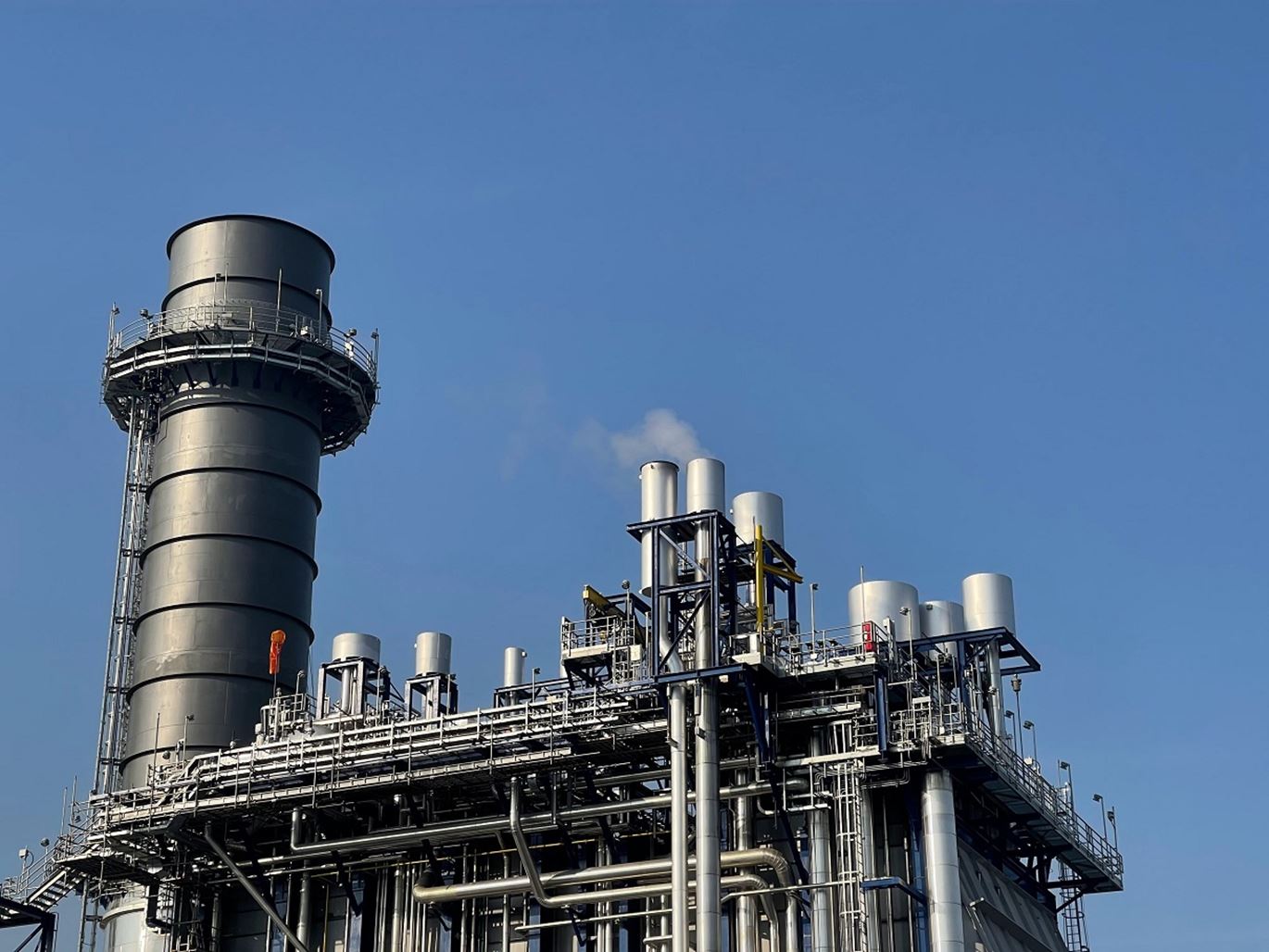
Jak wygląda proces produkcji płytek ceramicznych?
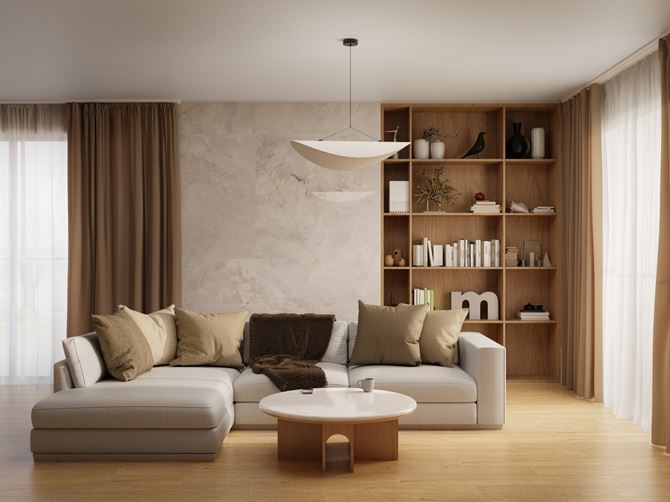
Etapy produkcji
- Minerały i surowce sypkie, z których powstają płytki, takie jak sproszkowana glina, piasek czy talk, składowane są w specjalnych boksach. Następnie zależnie od tego, jakiemu cyklowi produkcyjnemu będą poddawane, trafiają do odpowiednich wagozasilaczy. Odmierzane są w nich dokładne proporcje składników na podstawie starannie opracowanych przez technologów receptur.
Po stworzeniu odpowiedniej mieszanki, trafia ona do potężnych młynów kulowych. W nich składniki mielone są na mokro, przy dodatku ok. 30% wody. W ten sposób uzyskuje się masę lejną, która poddawana jest homogenizacji. Ten proces ujednorodnienia jest prowadzony przy pomocy mieszadeł znajdujących się w zbiornikach, które nieprzerwanie pracują, w związku z tym, iż masa ta musi być nieustannie mieszana. Ponadto, przy użyciu specjalnych pigmentów można ją zabarwić na wybrane kolory.
W kolejnym etapie wytwarzany jest zasadniczy surowiec niezbędny do wyprodukowania płytek, czyli granulat ceramiczny. Powstaje on w wyniku poddawania leiwa procesowi suszenia. Za pomocą gorących gazów spalinowych odparowywany jest nadmiar wody, uzyskując wilgotność na poziomie ok. 5%. Dla zachowania ciągłości produkcji uzyskany prefabrykat przechowuje się w silosach, a dalsze czynności mają miejsce na niezależnych liniach produkcyjnych.
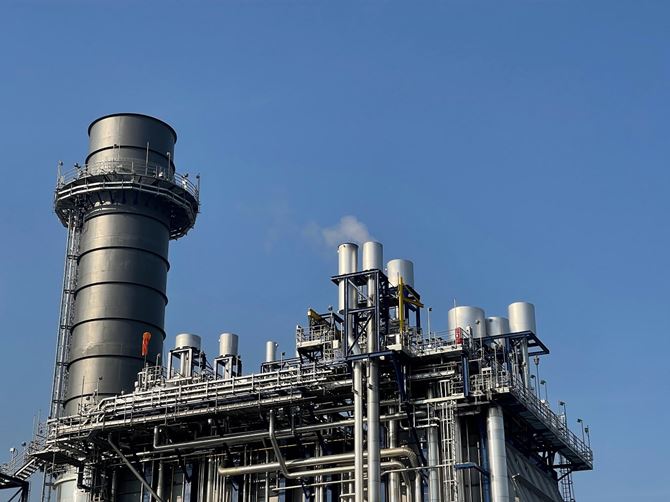
- Uzyskany granulat kierowany jest do pras. To moment, w którym poprzez ciśnienie 25-300 kg/cm2 i nacisk tłoka ok. 900-1500 ton nakładany na znajdujący się w formie prefabrykat, uzyskuje się kształt i rozmiar płytek ceramicznych, co zależne jest od zamontowanych w prasie stempli. Prasowanie płytek wykonywane jest dwukrotnie w celu zapobiegania pozostania powietrza wewnątrz płytki. Także na tym etapie ma miejsce suszenie, które służy obniżeniu wilgotności otrzymanej masy. Tym samym zwiększana jest wytrzymałość płytek, co usprawnia transport, ich dalszą obróbkę oraz minimalizuje ryzyko uszkodzenia podczas procesu wypalania. Podczas pobytu w suszarni podgrzewa się je również do odpowiedniej temperatury.
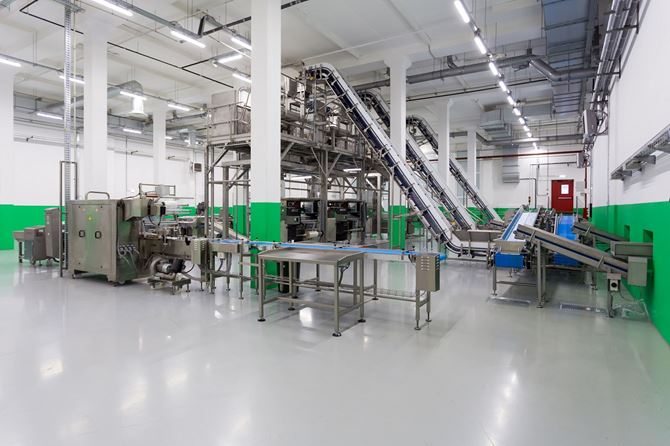
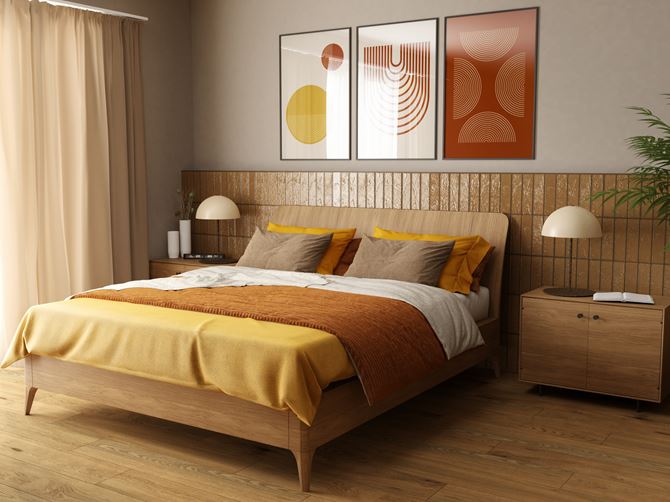
- Zanim płytki ceramiczne trafią do wypalania, nanosi się na nie odpowiednią powierzchnię oraz nadruk, a w przypadku płytek szkliwionych również szkliwo. Czynione jest to najczęściej za pomocą metalizatorów, drukarek cyfrowych oraz granili.
Dosuszone płytki ceramiczne zostają wprowadzone do pieców, gdzie są poddawane wysokiej temperaturze. Piece sterowane są specjalnymi systemami komputerowymi, które stopniowo podnoszą temperaturę, dostosowując ją rodzaju produkowanej płytki. Po osiągnięciu temperatury maksymalnej, w okolicy 1200 C, jest ona stopniowo obniżana.
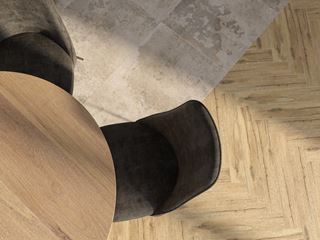
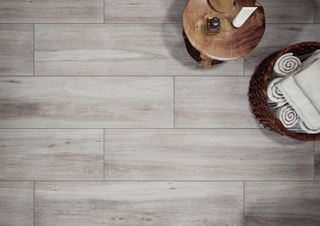
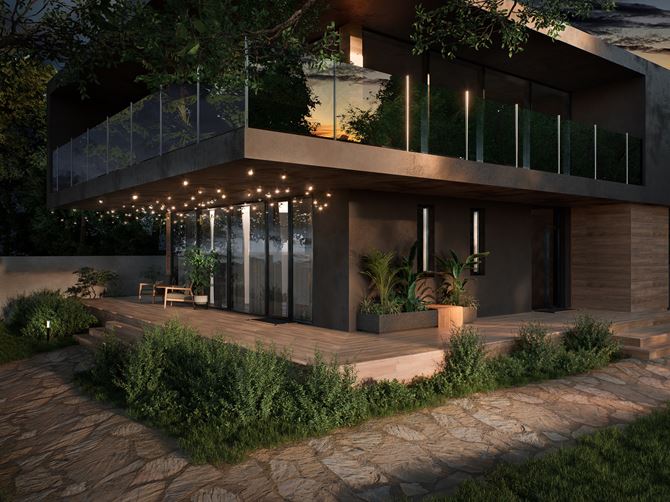
Każda płytka, która zejdzie z linii produkcyjnej, poddawana jest kontroli jakości według odgórnie ustalanych norm. Bada się między innymi takie parametry jak zgodność wymiarów, odporność na zginanie czy płaskość powierzchni. Następnie trafiają one do sortowacza, który naocznie ocenia i wykrywa ewentualne wady powierzchni. Płytki ocenione pozytywnie kierowane są do automatycznej sortowni.
- Gotowe płytki porządkowane są według odpowiedniego gatunku, kalibru czy partii produkcyjnych, po czym pakuje się je do oznakowanych kartonów. Umieszcza się je na paletach i zabezpiecza folią. Tak zabezpieczone są gotowe do opuszczenia fabryki i trafiają do sklepów lub magazynów.
Polecane artykuły:
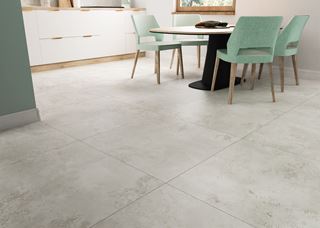
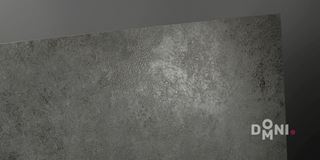